¿Cuándo reemplazar un repuesto industrial?
¿Cómo saber cuándo es momento de cambiar un repuesto en una máquina?
El correcto funcionamiento de las máquinas es esencial para mantener la productividad industrial de una empresa; la estabilidad de toda la organización puede depender de ello.
Los repuestos, que son piezas clave para el desempeño de las máquinas, tienen obviamente una vida útil limitada, y saber, a través del mantenimiento preventivo cuándo es el momento adecuado para reemplazarlos es fundamental para evitar fallos inesperados y costosos.
Para ello, se deben considerar diversos factores técnicos que permitan una evaluación precisa del desgaste y la efectividad de los componentes.
1. Monitoreo del Desempeño de la Máquina

Uno de los indicadores más claros de que un repuesto está cerca de su vida útil es la disminución en el desempeño general de la máquina.
Esto incluye un aumento en los tiempos de ciclo, reducción en la velocidad de producción, o caída en la calidad del producto. Si un componente específico como una correa, rodamiento o bomba ya no está funcionando de manera eficiente, la máquina podría estar operando por debajo de su capacidad óptima.
Este tipo de pérdidas de eficiencia no solo impactan la producción, sino que también pueden generar sobrecalentamientos y daños a otros componentes si no se abordan a tiempo.
2. Análisis de Vibraciones
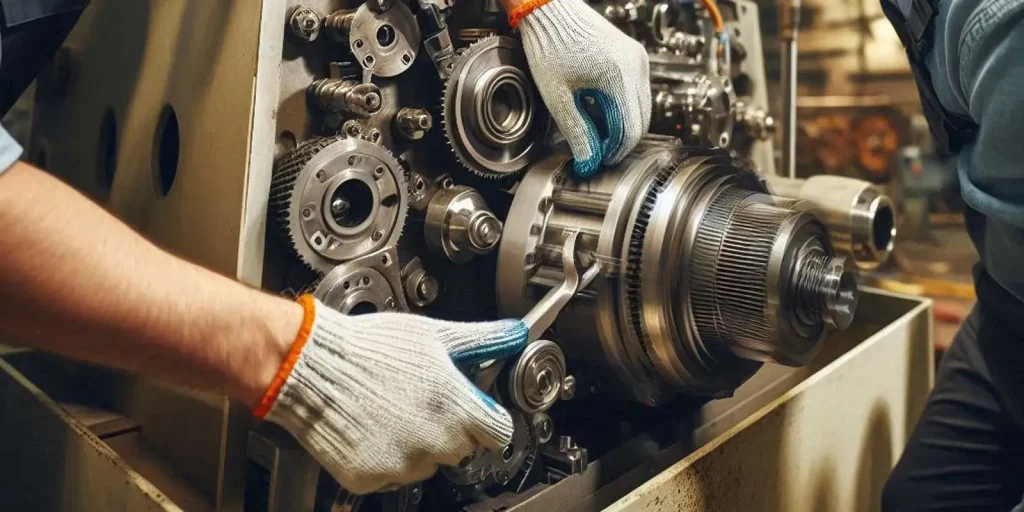
El análisis de vibraciones es una técnica ampliamente utilizada en mantenimiento predictivo para identificar problemas en componentes rotatorios o en máquinas con partes móviles.
Los sensores de vibración pueden detectar alteraciones en los patrones vibratorios normales, lo cual es una señal de que un repuesto, como un rodamiento o un engranaje, podría estar desgastado o dañado.
Las vibraciones anormales pueden indicar desbalance, desalineación, desgaste o incluso fracturas internas en los componentes.
El monitoreo continuo de las vibraciones puede predecir fallos antes de que ocurran, permitiendo planificar el reemplazo del repuesto con antelación.
3. Temperaturas Anómalas
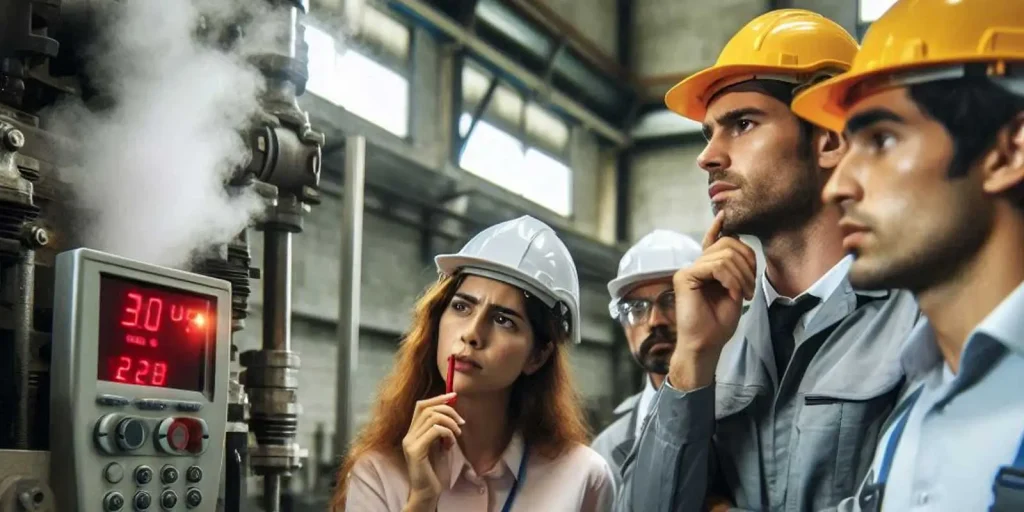
Las variaciones en la temperatura de funcionamiento de las máquinas son otro indicio claro de que un repuesto puede estar llegando al final de su vida útil.
Los componentes que sufren desgaste o mal funcionamiento, como bombas, motores o rodamientos, tienden a generar más calor del habitual.
Un aumento de temperatura excesivo puede ser signo de fricción interna, mala lubricación o deterioro de materiales, lo que puede acelerar el desgaste de otras piezas y provocar fallos catastróficos si no se reemplaza el repuesto afectado.
El monitoreo de temperaturas con sensores infrarrojos o termográficos es una herramienta eficaz para detectar estos problemas a tiempo.
4. Inspección Visual y Física
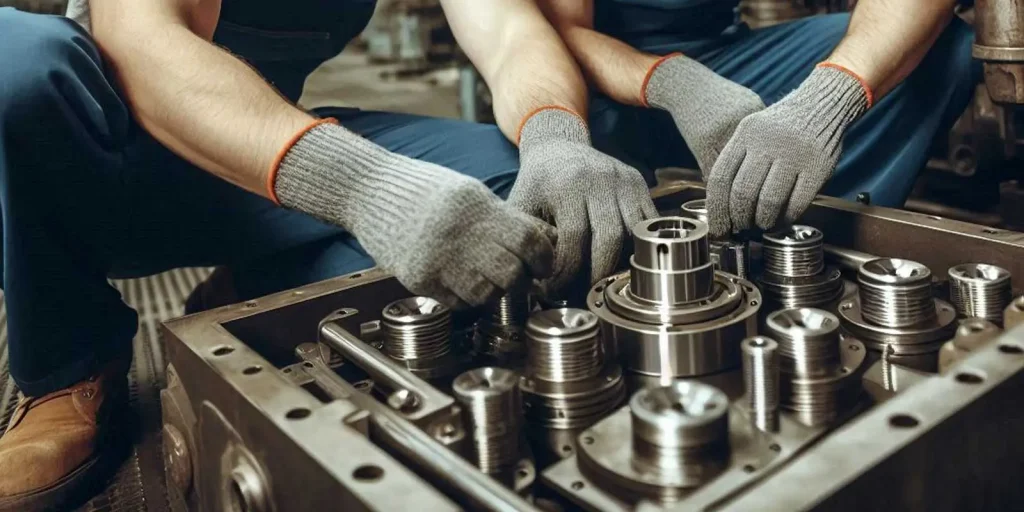
Una inspección visual regular es una de las técnicas más sencillas pero efectivas para identificar el desgaste o daño de un repuesto. Se debe verificar la presencia de grietas, deformaciones, corrosión, fisuras o acumulación de residuos que puedan afectar el rendimiento del componente.
Por ejemplo, una correa desgastada o un engranaje con dientes dañados no solo comprometen el funcionamiento de la máquina, sino que pueden provocar un fallo completo si no se reemplazan a tiempo.
Además, es importante revisar el estado de los sellos y juntas, ya que su desgaste puede provocar fugas de fluidos o pérdidas de presión, afectando la eficiencia de la maquinaria.
5. Monitoreo de Horas de Operación y Registros de Mantenimiento
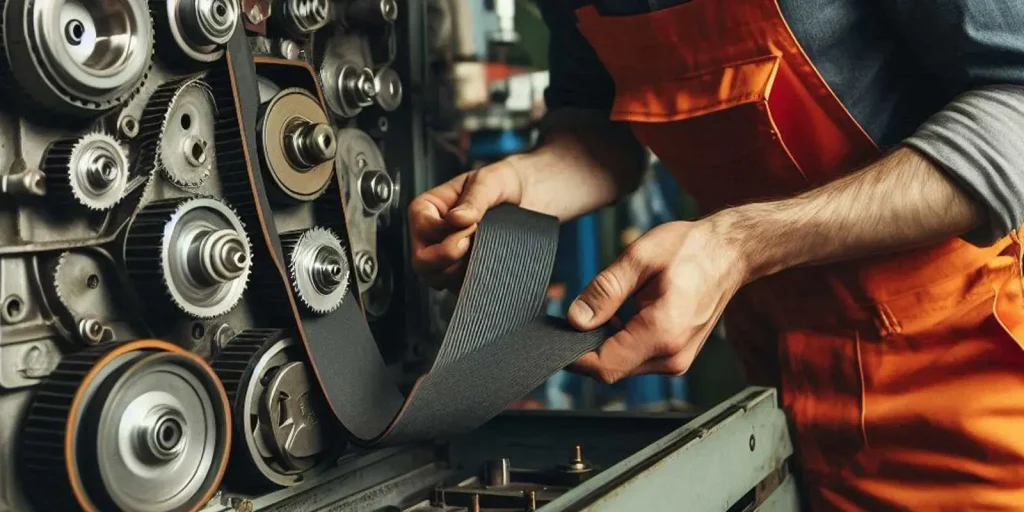
La gestión del ciclo de vida de los repuestos también depende del seguimiento riguroso de las horas de operación de la máquina y los registros de mantenimiento.
Cada componente tiene una vida útil calculada en función del tiempo o de las horas de operación bajo condiciones específicas. El mantenimiento preventivo basado en el fabricante y los datos históricos de uso puede prever el momento óptimo para el reemplazo de los repuestos, evitando el desgaste excesivo.
Las plataformas de mantenimiento basadas en software pueden automatizar este proceso, alertando sobre la necesidad de reemplazo de los componentes en función de su ciclo de vida estimado.
6. Análisis de Fallas y Comportamiento de Componentes

El análisis de fallas es esencial cuando un repuesto muestra signos de mal funcionamiento repetitivo, incluso después de realizar ajustes o reparaciones.
Si un componente sigue fallando a pesar de haber sido reparado o mantenido, esto indica que está alcanzando su límite de operatividad y debería ser reemplazado.
Los análisis de fallas pueden incluir inspección microscópica, pruebas de materiales o análisis de residuos y contaminantes en los fluidos, con el fin de obtener información precisa sobre el estado del repuesto y determinar si está causando o es susceptible a daños adicionales.
7. Factores Ambientales y de Operación

Además de los factores mecánicos y de desempeño, las condiciones ambientales en las que opera la máquina también influyen en la durabilidad de los repuestos.
Exposición a temperaturas extremas, humedad, corrosión o cargas de trabajo más altas de lo previsto pueden acelerar el desgaste de los componentes. Por ejemplo, en entornos industriales donde se manejen líquidos corrosivos o se produzca polvo en exceso, los repuestos pueden degradarse más rápidamente y requerir sustitución más frecuente.
Conclusión
El reemplazo oportuno de repuestos industriales es esencial para mantener la eficiencia operativa, evitar paradas no planificadas y optimizar los costos de mantenimiento.
Implementar una estrategia de mantenimiento predictivo y preventivo basada en monitoreo constante de variables como el desempeño, las vibraciones, las temperaturas y el estado físico de los componentes es crucial.
Además, el uso de tecnologías avanzadas como sensores inteligentes, software de monitoreo y análisis de fallas ayuda a prever el desgaste de los repuestos antes de que se produzcan fallos costosos, permitiendo una gestión más eficiente y menos disruptiva de las operaciones industriales.

